Sept. 12th, 2024, Krosno, Poland
- 80 Years of History
- New challenges for the plant going forward
- Supplying suspension products to major OEMs globally
On September 12th, current and former employees, BWI Group management and invited guests took part in the celebration of the 80th anniversary of the shock absorber factory in Krosno. The plant is today not only one of the largest production facility in the BWI Group, but is also, with impressive statistics and decades of experience, a proven and reliable partner supplying globally the automotive industry with innovative suspension solutions.
„Our strength comes from values we stay aligned with. Innovation, quality and customer care are the pillars on which we have built our reputation”. says Dariusz Kucza, Plant Director.
80 Years of History
The beginning of the plant is back to 1944. After years of wartime turmoil, workers returned to the destroyed rubber factory to restore production and revive the spirit of the industry, so much needed in Poland at that time. Initially, the activity was focused on the repair of agricultural equipment. By the end of the 1950s, the Polish government decided to narrow down the production to the manufacturing of spring elements for motorcycles and telescopic shock absorbers. In 1958, the first shock absorber was produced in the Krosno factory, and in 1969 the site was officially named POLMO. In 1997, the American Company Delphi Automotive Systems took over the facility. Under this new name, Krosno plant acquired new customers and modernized its production processes. The development and strengthening of the plant continued with a redoubled intensity when BWI Group became the new owner of the site in 2009.
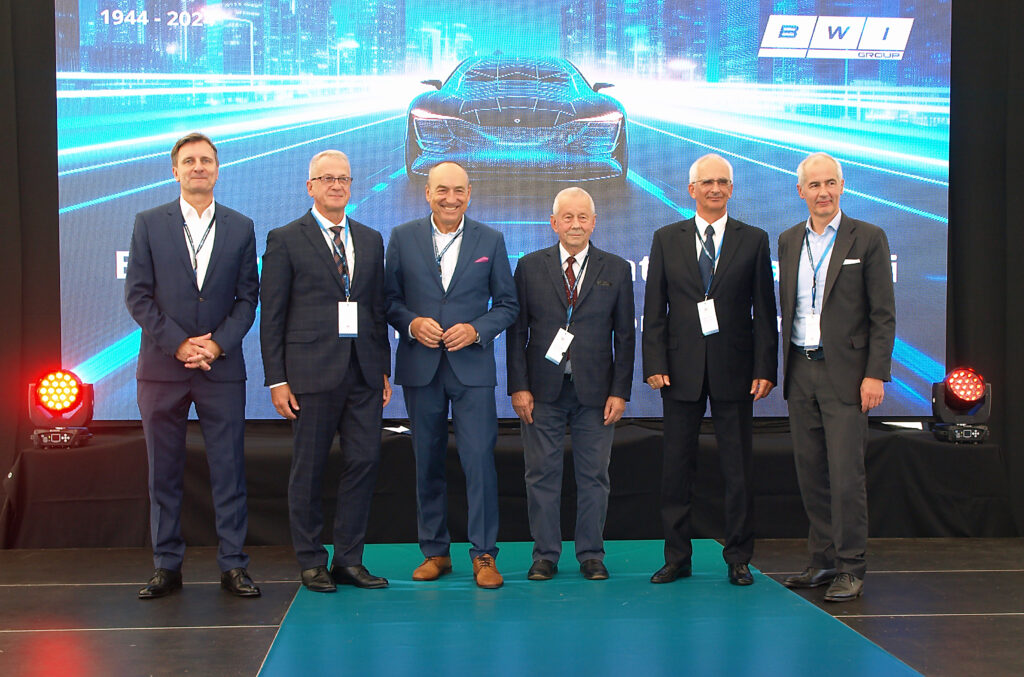
New challenges
80 years of existence makes the Krosno factory not only the witness of the history, but also shows the transformation that Poland went thru the last eight decades. During the post-war time, there was a giant demand for reviving the industry, while facing a lack of resource and tools required for an efficient operation. Then came the time of privatization of the industry by the end of the 20th century, when foreign capital and modern technologies entered Polish industry. Today in the hands of BWI Group, the manufacturing facility entered into a new chapter with operation based on Manufacturing 4.0 solutions, the highest quality standards and the newly adopted Sustainability policy. In this regard, the plant began its transformation last year towards 50 percent reduction electricity carbon emissions, as well as a 15 percent reduction in production waste by the end of 2024.
Today’s Products and Customers
The factory is currently supplying to major OEMs automotive suspension components, including various shock absorbers and struts, controlled dampers such as MagneRide® dampers, Semi-Active Roll Control systems, Magneto-Rheological engine mounts, but also Electronic Control Units and sensors, which enhances the BWI Group’s ability to develop electronic and electrical architectures. Krosno is delivering to 46 customers in 97 locations worldwide. Among these customers are BMW, Stellantis, Ford, GM, Audi, Volvo, VW, Ferrari and Lamborghini.
The plant in Krosno is one of the largest employers in the Sub-Carpathian region, and its long history makes it also one of the most recognizable and significant industry company of the Polish economy. With more than 300 million units produced since its debut, the plant has not only gone thru the history of industrial development in Poland, but also contributed to it.
“None of our successes would have been possible without the people who made and make this plant. Let me express my great gratitude to all – employees, both those who have been with us for years and those who have joined us recently. It is their hard work, commitment and loyalty that are the foundation of our success.” adds Plant Director expressing his gratitude towards the Staff.
About BWI Group
BWI Group’s is one of the market leader with high quality brake and suspension products and have been recognized by more than 50 global automakers. Thanks to the progress on technological breakthroughs, business development, and production, The company’s total order value rocketed by nearly 300% year-on-year in 2023. The company’s solid development has benefited from the integration of its global resources from three continents, Asia, Europe and North America, to empower global smart mobility. With a heritage reaching back over 100 years, BWI Group is now operating a total of 9 production bases, 7 research and development centers, and 1 software center worldwide.